Tate & Lyle building biomass boiler to slash carbon emissions of London sugar refinery by 70%
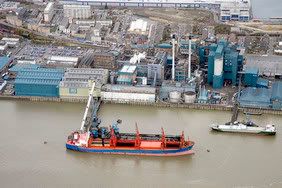
The new biomass boiler, which will power the combined heat and power (CHP) plant for the factory, will mean Tate & Lyle can switch to renewable biomass to supply 70% of the energy it needs. Post 2009, with the boiler working at full capacity, the carbon footprint of cane sugar produced at the UK refinery will be reduced to 0.32 tonnes per 1 tonne of sugar.
Raw cane sugar milling is almost carbon neutral. Cane grows in the field, waste fibre from the cane (bagasse) powers the factory and the cane re-grows each year, often up to 10 times without the need for replanting since sugar cane is a semi-perennial. The raw sugar is then transported by Tate & Lyle to its UK refinery by ships, widely regarded as the most energy efficient mode of transport only producing very small levels of CO2 emissions per ton shipped.
The total capacity of the biomass boiler at the Thames plant will be 65MW. It will generate 80 tons of steam per hour at 45 bar (650psi) pressure and will run 24/7. The feedstock for the boiler will be wheat feed, a by-product of flour production. The factory will become a net exporter of energy to the grid with the biomass scheme ensuring this excess electricity is green.
Tate & Lyle also hopes to recycle the estimated 6,500 tonnes of ash from the boiler as a base for fertiliser or for use in the construction of building blocks, rather than going to landfill (more on utilising biomass ash as a construction material, see here).
Having recently confirmed what we’d already anticipated, that our carbon footprint is low at 0.43 tonnes per 1 tonne of sugar, we are now proud to be taking steps to reduce that even further with this project. This is more than a pledge - it's happening now, with construction already started. Furthermore, we believe the boiler being constructed at our Thames site is not only the largest of its kind for London, but also a first for the UK food and drink industry. At Tate & Lyle we have an overall target to reduce energy consumption by 3% per annum and this has been in place since 2000. In addition, we are currently a net-exporter to the National Grid at the refinery and once the biomass project is complete, the source will be green. - Ian Bacon, Chief Executive Tate & Lyle SugarsTate & Lyle’s carbon footprint was calculated by URS Corporation Ltd., an independent consultancy in carbon measurement, who have developed a tool to measure the carbon footprint of both the UK cane sugar refinery as well as the entire cane sugar production process from field to leaving the factory gates:

Key stages of URS’ methodology included:
- Understanding the manufacturing process from raw material production through to distribution
- Developing a process map to identify each of the inputs and outputs of each stage including utility use as well as raw materials
- Defining the boundaries and scope of the footprint
- Data collection
- Data processing and calculation
The planned 70% reduction in CO2 emissions associated with energy use is significant by any standards. Indeed, it is exemplary. It is exactly the sort of change in behaviour that FDF is encouraging under our Five-fold Environmental Ambition launched last month. If more companies follow Tate & Lyle’s example, a low carbon economy will quickly cease to be an aspiration and become a reality. - Callton Young, Director of Sustainability and Competitiveness at the Food & Drink FederationEfforts to reduce carbon emissions at the Thames refinery are part of Tate & Lyle's group-wide environmental and energy saving measures, which has seen energy consumption per unit of output reduced by 1.2%; water consumption per unit of output reduced by 2.5%; and non hazardous solid waste consumption per unit of output reduced by 29.5% in the last year (calendar year 2006).
Tate & Lyle is a leading manufacturer of renewable food and industrial ingredients. It uses innovative technology to transform corn and sugar into value-added ingredients for customers in the food, beverage, pharmaceutical, cosmetic, paper, packaging and building industries. The Company is a leader in cereal sweeteners and starches, sugar refining, value added food and industrial ingredients, and citric acid. Tate & Lyle is the world number-one in industrial starches and is the sole manufacturer of SPLENDA Sucralose.
Headquartered in London, Tate & Lyle operates more than 50 production facilities throughout Europe, the Americas and South East Asia. In the year to 31 March 2007, it employed 6,900 people in its subsidiaries with a further 2,300 employed in joint ventures. Sales in the year to 31 March 2007 totalled £4.0 billion.
References:
Tate & Lyle: The Future's green for Tate & Lyle - November 26, 2007.
Biopact: The bioeconomy at work: buildings made of biomass ash? - May 17, 2007
0 Comments:
Post a Comment
Links to this post:
Create a Link
<< Home