Syntroleum announces successful completion of CTL demonstration; important for BTL technology and carbon-negative biofuels
Syntroleum Corporation, a synthetic fuels technology company, has successfully completed a demonstration of its proprietary technology designed to convert coal into clean synthetic liquid fuels. The test run utilized synthesis gas produced from coal and Syntroleum's proprietary cobalt catalyst technology in the conversion process. The 2,500-hour bench-scale test run was recently completed at Eastman Chemical Company's Kingsport, Tennessee facility.
Syntroleum says the demonstration is a very important step towards the development of biomass-to-liquids (BTL) processes resulting in synthetic biofuels. Importantly, because the cobalt catalyst used by Syntroleum localizes carbon capture to the shift reactor syngas product, it allows for easier CO2 capture and sequestration. With BTL technology combined with carbon capture and storage (CCS), a whole range of new bioenergy opportunities becomes available, including the production of carbon-negative biofuels. Unlike ordinary biofuels or renewables like wind or solar, which are merely 'carbon-neutral', these 'negative emissions' fuels take historic CO2 emissions back out of the atmosphere (earlier post).
Syntroleum's demonstration proved that fuels made from coal have the same superior synthetic Fischer-Tropsch (FT) qualities as those made from natural gas. The demonstration also indicated that Syntroleum's proprietary cobalt-based catalyst performs robustly under real-world coal-to-liquids (CTL) conditions, as was predicted from earlier extended life tests performed by Syntroleum.
The two major process steps in CTL (and GTL, BTL) production consist of gasification and Fischer-Tropsch synthesis (schematic, click to enlarge). After these steps, the liquids are further refined.
Gasification
A gasifier converts coal feedstock into gaseous components by applying heat and pressure to the coal in the presence of steam and oxygen. A gasifier differs from a combustor in that the amount of oxygen inside the gasifier is carefully controlled such that only a relatively small portion of the fuel burns completely, minimizing the formation of carbon dioxide:
energy :: sustainability :: biomass :: bioenergy :: biofuels :: coal-to-liquids :: gasification :: syngas :: Fischer-Tropsch :: biomass-to-liquids :: carbon-negative :: carbon capture and storage :: synthetic biofuels ::
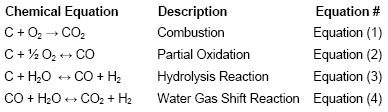
The combustion and gasification reactions are shown in Eq 1 and Eqs 2-4 respectively. The reaction of Eq 2 is termed partial oxidation. Rather than burning, most of the carbon-containing feedstock is chemically broken apart by the gasifier’s heat and pressure producing syngas. Water introduced into the gasifier also takes part in the chemical decomposition of coal, producing carbon oxides and hydrogen as in Eq 3-4.
The produced syngas is primarily hydrogen and carbon monoxide with other gaseous components. The actual composition depends on the conditions in the gasifier and the type of feedstock. Typical coal syngas H2:CO ratios are in the 0.4:1 to 0.9:1 range. For FT conversion, the desired ratio is 2.1:1. “Ratio adjustment” via the water-gas shift reaction of Eq 4 is thus required to convert syngas to FT hydrocarbons. This may be done in the gasifier, a catalytic shift converter, or the FT reactor itself by using catalysts with water-gas shift selectivity (e.g. iron). For optimum operation of the gasifier and the FT reactor, the preferred option is the catalytic shift converter.
This has the added advantage of eliminating CO2 from FT reactor tail gas and simplifying carbon capture. All CO2 is captured after water-gas shift as part of syngas cleanup.
Note - this is where the potential of carbon-negative biofuels comes in: when the CO2 from the process is captured from an already renewable feedstock - biomass - and then geosequestered, the result is a negative emissions fuel that takes historic CO2 emisions out of the atmosphere as it is used.
Other major gaseous components found in the syngas stream are derived from the sulfur and nitrogen containing compounds found in coal. In addition to the sulfur and nitrogen components the syngas may contain metals, e.g. mercury and arsenic. The metals, sulfur and reactive nitrogen compounds are removed from the gasifier effluent to provide clean syngas for further processing. Non-combustible components e.g. calcium and silicon, typically leave the bottom of the gasifier as slag.
Fischer-Tropsch Conversion
The FT process uses a catalyst to convert syngas to hydrocarbon products according to the general chemical pathway given by the following equation:

There is a distribution of intermediate feedstocks generated during this FT chemical process including unreacted gases, short and long chain paraffins, olefins and alcohols. The type of catalyst and operating conditions impact the distribution of the intermediate feedstocks generated.
Standard refinery hydroprocessing and fractionation is used to convert the raw chemicals generated into commercial products, primarily transportation fuels. The unconverted syngas and light gas products in the reactor tail gas are used for internal power generation as shown in the schematic.
Tests
Eastman Chemical Company and Syntroleum Corporation have developed their respective technologies and expertise independently. The companies combined their experience to demonstrate that coal can be effectively converted to liquid hydrocarbons with a cobalt based FT catalyst.
FT catalysts have historically been based on iron or cobalt. While iron catalyst requires a lower initial investment, cobalt has numerous performance advantages such as higher activity, higher diesel yields, longer life, and lower water gas shift activity resulting in lower overall operating cost. The higher activity and longer life of cobalt catalyst offsets the initial higher cost.
By not causing water-gas shift in the FT reactor, cobalt catalysts localize carbon capture (CO2 sequestering) to the shift reactor syngas product. The CO2-concentrated syngas may effectively be scrubbed as part of the cleanup process shown in the schematic. Exposure to contaminants increases with the longer life of the cobalt catalyst resulting in increased potential for catalyst deactivation. Therefore cobalt catalyst must be designed consistent with commercially available syngas cleanup processes.
Syntroleum has invested over one million hours of run time in bench scale FT catalyst tests, much of it in Continuous Stirred Tank Reactors (CSTR) like those used in the present study. These tests include extensive studies on trace levels of various contaminants and a patented regeneration process. Syntroleum's regeneration process separates the catalyst from the wax matrix returning it to the original oxide form. The catalyst is then re-reduced, slurried and returned to the reactor.
This procedure has been demonstrated at lab, pilot, and demonstration scale, restoring catalyst activity from a wide range of deactivation mechanisms. With this background, Syntroleum was able to establish a maximum target level of contaminants in the syngas and designed guard beds through which syngas produced at the Eastman facility was processed. The combined experience of the two companies was essential in the success of the demonstration program.
Data on the gasification and FT demonstration can be found in a non confidential White Paper.
Jet fuels
These results in conjunction with the Air Force's successful testing of Syntroleum's Fischer-Tropsch jet fuel last fall and the recent certification of FT jet fuel for the B-52 H Stratofortress bomber create an opportunity for Syntroleum to supply synthetic jet fuel from several sources to help the Air Force meet its target of providing 50 percent of its needs with a 50/50 synthetic blend by 2016.
As previously announced, Syntroleum has contracted to deliver 500 gallons of renewable synthetic jet fuel for testing by the Air Force. This fuel will be made using Syntroleum proprietary Biofining(TM) technology using a mixture of low grade animal fats and greases as provided by Tyson Foods.
Based on preliminary testing, Syntroleum believes this renewable fuel has almost identical properties to the natural gas-based FT jet fuel used in the certification tests.
References:
Syntroleum: White Paper: Fischer Tropsch Catalyst Test on Coal-Derived Synthesis Gas - s.d. [November 2007].
Syntroleum: Syntroleum Announces Successful Completion of Coal-to-Liquids Demonstration - November 8, 2007.
Biopact: A quick look at 'fourth generation' biofuels - October 08, 2007
Biopact: Syntroleum to deliver bio-based synthetic jet fuel to U.S. Department of Defense - July 09, 2007
Syntroleum says the demonstration is a very important step towards the development of biomass-to-liquids (BTL) processes resulting in synthetic biofuels. Importantly, because the cobalt catalyst used by Syntroleum localizes carbon capture to the shift reactor syngas product, it allows for easier CO2 capture and sequestration. With BTL technology combined with carbon capture and storage (CCS), a whole range of new bioenergy opportunities becomes available, including the production of carbon-negative biofuels. Unlike ordinary biofuels or renewables like wind or solar, which are merely 'carbon-neutral', these 'negative emissions' fuels take historic CO2 emissions back out of the atmosphere (earlier post).
Syntroleum's demonstration proved that fuels made from coal have the same superior synthetic Fischer-Tropsch (FT) qualities as those made from natural gas. The demonstration also indicated that Syntroleum's proprietary cobalt-based catalyst performs robustly under real-world coal-to-liquids (CTL) conditions, as was predicted from earlier extended life tests performed by Syntroleum.
We have now proven that the Syntroleum Process, and specifically our cobalt catalyst, performs very well on live coal syngas in a commercial environment. This is a great step for Syntroleum and we continue to believe that this technology will help pave the way to lowering our country's reliance on foreign sources of oil, by producing domestically sourced synthetic diesel and jet fuel. This successful demonstration under the most challenging condition of live coal derived syngas is also very important for the future of our Biomass-to-Liquids technology. - Jack Holmes, CEO of Syntroleum.By showing that live coal derived syngas can be turned into liquids, biomass-to-liquids technology, which is less challenging, becomes a step closer. The syngas produced from gasifying such biomass feedstocks as corn stover, wood by-products, and chicken litter is more difficult to clean up than natural gas-based syngas (for gas-to-liquids production, GTL) but much easier than coal-based syngas. By demonstrating the commercial viability of its cobalt catalyst for coal, the company has addressed its suitability for any renewable feedstock.
The two major process steps in CTL (and GTL, BTL) production consist of gasification and Fischer-Tropsch synthesis (schematic, click to enlarge). After these steps, the liquids are further refined.
Gasification
A gasifier converts coal feedstock into gaseous components by applying heat and pressure to the coal in the presence of steam and oxygen. A gasifier differs from a combustor in that the amount of oxygen inside the gasifier is carefully controlled such that only a relatively small portion of the fuel burns completely, minimizing the formation of carbon dioxide:

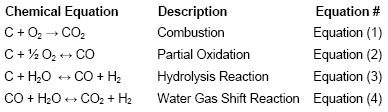
The produced syngas is primarily hydrogen and carbon monoxide with other gaseous components. The actual composition depends on the conditions in the gasifier and the type of feedstock. Typical coal syngas H2:CO ratios are in the 0.4:1 to 0.9:1 range. For FT conversion, the desired ratio is 2.1:1. “Ratio adjustment” via the water-gas shift reaction of Eq 4 is thus required to convert syngas to FT hydrocarbons. This may be done in the gasifier, a catalytic shift converter, or the FT reactor itself by using catalysts with water-gas shift selectivity (e.g. iron). For optimum operation of the gasifier and the FT reactor, the preferred option is the catalytic shift converter.
This has the added advantage of eliminating CO2 from FT reactor tail gas and simplifying carbon capture. All CO2 is captured after water-gas shift as part of syngas cleanup.
Note - this is where the potential of carbon-negative biofuels comes in: when the CO2 from the process is captured from an already renewable feedstock - biomass - and then geosequestered, the result is a negative emissions fuel that takes historic CO2 emisions out of the atmosphere as it is used.
Other major gaseous components found in the syngas stream are derived from the sulfur and nitrogen containing compounds found in coal. In addition to the sulfur and nitrogen components the syngas may contain metals, e.g. mercury and arsenic. The metals, sulfur and reactive nitrogen compounds are removed from the gasifier effluent to provide clean syngas for further processing. Non-combustible components e.g. calcium and silicon, typically leave the bottom of the gasifier as slag.
Fischer-Tropsch Conversion
The FT process uses a catalyst to convert syngas to hydrocarbon products according to the general chemical pathway given by the following equation:

Standard refinery hydroprocessing and fractionation is used to convert the raw chemicals generated into commercial products, primarily transportation fuels. The unconverted syngas and light gas products in the reactor tail gas are used for internal power generation as shown in the schematic.
Tests
Eastman Chemical Company and Syntroleum Corporation have developed their respective technologies and expertise independently. The companies combined their experience to demonstrate that coal can be effectively converted to liquid hydrocarbons with a cobalt based FT catalyst.
FT catalysts have historically been based on iron or cobalt. While iron catalyst requires a lower initial investment, cobalt has numerous performance advantages such as higher activity, higher diesel yields, longer life, and lower water gas shift activity resulting in lower overall operating cost. The higher activity and longer life of cobalt catalyst offsets the initial higher cost.
By not causing water-gas shift in the FT reactor, cobalt catalysts localize carbon capture (CO2 sequestering) to the shift reactor syngas product. The CO2-concentrated syngas may effectively be scrubbed as part of the cleanup process shown in the schematic. Exposure to contaminants increases with the longer life of the cobalt catalyst resulting in increased potential for catalyst deactivation. Therefore cobalt catalyst must be designed consistent with commercially available syngas cleanup processes.
Syntroleum has invested over one million hours of run time in bench scale FT catalyst tests, much of it in Continuous Stirred Tank Reactors (CSTR) like those used in the present study. These tests include extensive studies on trace levels of various contaminants and a patented regeneration process. Syntroleum's regeneration process separates the catalyst from the wax matrix returning it to the original oxide form. The catalyst is then re-reduced, slurried and returned to the reactor.
This procedure has been demonstrated at lab, pilot, and demonstration scale, restoring catalyst activity from a wide range of deactivation mechanisms. With this background, Syntroleum was able to establish a maximum target level of contaminants in the syngas and designed guard beds through which syngas produced at the Eastman facility was processed. The combined experience of the two companies was essential in the success of the demonstration program.
Data on the gasification and FT demonstration can be found in a non confidential White Paper.
Jet fuels
These results in conjunction with the Air Force's successful testing of Syntroleum's Fischer-Tropsch jet fuel last fall and the recent certification of FT jet fuel for the B-52 H Stratofortress bomber create an opportunity for Syntroleum to supply synthetic jet fuel from several sources to help the Air Force meet its target of providing 50 percent of its needs with a 50/50 synthetic blend by 2016.
As previously announced, Syntroleum has contracted to deliver 500 gallons of renewable synthetic jet fuel for testing by the Air Force. This fuel will be made using Syntroleum proprietary Biofining(TM) technology using a mixture of low grade animal fats and greases as provided by Tyson Foods.
Based on preliminary testing, Syntroleum believes this renewable fuel has almost identical properties to the natural gas-based FT jet fuel used in the certification tests.
References:
Syntroleum: White Paper: Fischer Tropsch Catalyst Test on Coal-Derived Synthesis Gas - s.d. [November 2007].
Syntroleum: Syntroleum Announces Successful Completion of Coal-to-Liquids Demonstration - November 8, 2007.
Biopact: A quick look at 'fourth generation' biofuels - October 08, 2007
Biopact: Syntroleum to deliver bio-based synthetic jet fuel to U.S. Department of Defense - July 09, 2007
1 Comments:
Based on preliminary testing, Syntroleum believes this renewable fuel has almost identical properties to the natural gas-based FT jet fuel used in the certification tests.
Post a Comment
Links to this post:
Create a Link
<< Home