A quick look at CNG ships
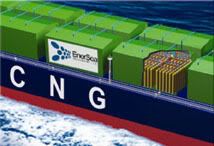
The latest innovations are important because the technology can also be used to transport biogas, a highly efficient carbon-neutral biofuel that can be made from dedicated energy crops. By looking at biogas as a 'stranded' gas reserve, a whole new range of energy options becomes available. Developing countries without natural gas resources but with good agro-climatic conditions for the production of biogas from energy crops could export to nearby markets with a growing demand for natural gas, and receive premium price for their carbon-neutral fuel. Unlike (stranded) natural gas, which has to be 'discovered', biogas projects can be carefully planned and located at the most optimal sites.

The feasibility of this concept - arguably the cleanest and most effective energy system to fight climate change - is currently being studied. The emergence of CNG ships makes it more promising. Versatile CNG tankers and strategically located biogas production could make for a perfect match.
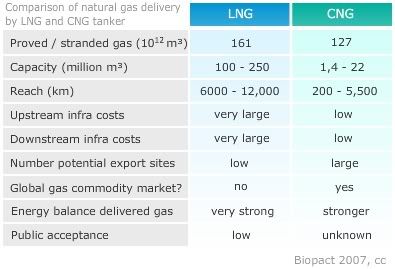
So who is developing CNG ships? And what kind of innovative technologies are being focused on? Five different companies are actively developing the concept: SeaNG, TransOcean Gas, and the Floating Pipeline Company, all from Canada, Norway's Knutsen OAS Shipping in collaboration with Det Norske Veritas and Europipe GmbH, and US company EnerSea Transport.
Three basic gas storage concepts are being looked at: (1) storing compressed gas in coselles - large coils of pipe wound into cylindrical storage containers -, (2) utilizing stacked pressure vessels (cylinders) made from light-weight composites, (3) moveable storage containers containing pipe sections, or steel or composite pressure vessels, that can be handled as an ordinary shipping container and can be blended into intermodal transport chains (rail and truck after delivery by ship). Let us have a closer look at these concepts.
COSELLE SYSTEM
SeaNG
SeaNG offers a solution for marine transport of natural gas over distances ranging from 200 to 2000 kilometers. Its CNG ships rely on the 'Coselle System' which is based on coiled pipe. SeaNG's Coselle CNG ship is the world’s first CNG ship to receive full classification approval.
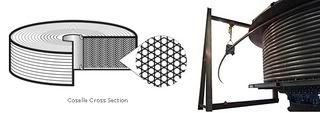

The size of a Coselle may range from 15 to 20 metres in diameter and 2.5 to 4.5 metres in height, and it may weigh about 550 tonnes. A single Coselle carries about 3.0 million standard cubic feet (mmscf) of natural gas, depending on Coselle dimensions, and gas temperature, pressure and composition. The Coselles are connected by a proprietary manifold and control system.
The complete Coselle CNG delivery system consists of a ship combined with loading and offloading facilities. The gas is compressed at a loading terminal (onshore or offshore) and loaded into a CNG ship. The ship then travels to the offloading terminal (onshore or offshore) where the gas is decompressed and delivered to market.
The Coselle CNG Ships are designed for the safe and efficient carriage of compressed natural gas (CNG) in Coselles. Each Coselle carries about 3 mmscf of gas and can be stacked on the deck or in the holds of a ship. These stacked Coselles are then manifolded together using a system that allows for safe and efficient gas loading and unloading.
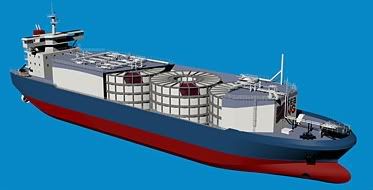
- 16 Coselle ship transporting about 50 mmscf of gas.
- 84 Coselle ship transporting about 250 mmscf of gas.
- 108 Coselle ship transporting about 325 mmscf of gas.
- 144 Coselle ship transporting about 450 mmscf of gas.
Coselles may also be loaded onto barges. However each barge would require an attendant tug while in harbour to comply with standard requirements of harbour authorities and international practice. Since there would be no efficiency gained by having fewer tugs than barges there would need to be compelling circumstances to use a tug barge system.
Knutsen OAS Shipping
Norway's Knutsen OAS Shipping collaborated with Det Norske Veritas (DNV), one of the leading experts on vessel design, pipeline design and safety assessment in the world, and with Germany's Europipe Gmbh, the leading pipeline fabrication company in the world to develop a similar concept consisting of pipes enclosed in cylindrical containers, but not wound like a coil. In this CNG concept the gas is stored under normal pressure in vertical cylinders on-board the vessel. The concept is based on several patents pending solutions. The 'pressurized natural gas' (PNG) system will not require sophisticated processing to maintain the gas stored in the containment system. Due to the operation under ambient temperatures, no isolation will be required to prevent heating during the voyage. The vertical cylinders will be prepared according to three main principles:
- design, material selection and testing regime for the cylinder is according to the recognised offshore pipeline code DNV-OS-F101 (similar to ISO/DIS 13623);
- end caps designed according to the International Gas Code (IGC) but with a minimum wall thickness not less than the cylinder wall; and
- all material used for cargo containment piping, cargo deck piping, valves and fittings is NV 316 or similar, complying with the requirements for manufacture survey and certification given by normal rules for classification of ships.
Knutsen OAS Shipping has worked jointly with Europipe GMBH in Germany to qualify the containment system according to new rules issued by DNV.
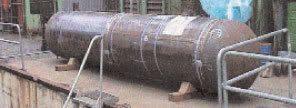
Full Scale Test Cylinder
Europipe has used the Mannesmann Research Institute and the containment system has been successfully qualified and approved by DNV according to the new DNV rules. This is an achievement that proves that CNG through the Knutsen PNG solution could become a reality. Europipe has already performed a trial production of the X-80 pipes and end caps according to PNG specification and DNV rules. These have been used for the qualification testing. Both fatigue and burst test has been performed. The fatigue test will ensure a PNG carrier lifetime of 40 years based on 50 loading per year. The burst test verified that sufficient burst capability remains in the cylinder even after a fatigue exposure of 40 years.Knutsen OAS Shipping has performed the vessel initial design with input from DNV and independent naval architect expertise. The vessels have been discussed with several of the major shipbuilding yards. The yard input together with the Europipe input for the containing system has given Knutsen the possibility to price the vessels to a detailed level necessary in order to be able to determine the unit cost for transportation of natural gas by PNG vessels.
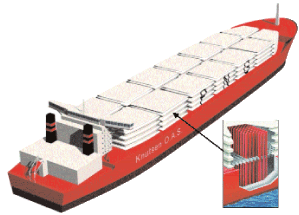
The offshore loading type vessel is based on Knutsen’s own experience with similar operation for oil. The vessel can apply the well-known submerged turret loading (STL) system from advanced production and loading (APL) systems. Other types of offshore loading systems are also being considered and detailed design and testing for a combined offshore/onshore loading and discharging system is on-going.
Several vessel sizes have been considered from small PNG carriers with gas carrying capacity down to 2–4MMSm3 to large PNG carriers with carrying capacity more that 30MMSm3.
The large size PNG carrier is capable of sailing with a speed of 17.5 knots and is very suitable for large volumes and/or long distance gas deliveries up to 3,000 nautical miles (nm). Similarly, smaller vessels can be built according to the volumes and distances required.
Gas transport using PNG vessels can be continuous if a minimum of three vessels is provided for gas transport from the gas source to the gas receiving part. More vessels can be added according to market demand, avoiding high initial tariff traditionally associated with other systems because of low utilisation.
Another advantage is that the gas quality that could be transported on PNG carriers are very similar to gas qualities allowed in pipeline systems. In fact, even richer gas could be transported in PNG carriers compared with pipelines, giving PNG carriers an advantage compared with LNG and even towards pipelines in some cases.
Compared with traditional LNG value chains, a PNG value chain would not require investments instorage and liquefaction facilities upstream and storage and regasification facilities downstream. This would make PNG an interesting new alternative for certain volumes/distances where LNG was previously considered the only option. Case studies indicate that for distances up to 3,000nm PNG could be more economic than LNG.
PNG offers an environmentally interesting solution. The vessel could be fuelled using natural gas, a favourable fuel compared with heavy fuel oils normally used in shipping – reducing the emissions of nitrogen oxides, carbon dioxide, sulphur and dust to the environment. Total energy demands are much less for PNG compared with LNG, while PNG, compared with pipeline, is very similar or better. Due to the heavy containment system, ballast water discharge would not be required. For some trades, this could be a very important environmental issue.
As part of the rule development, DNV performed a risk and safety assessment, that concluded that PNG transport is as safe as or even safer than comparable LNG transport – an important issue that must be considered when gas transport solutions are being established.
Because PNG delivery is performed with natural gas in gaseous phase, discharging could be far away from existing population. Discharging could even be performed offshore some distance from the shoreline and piped to shore. For some areas, this could be an advantage because of political risk or social unrest.
The PNG vessel operates at full pressure at ambient temperatures. This means that the containment system cannot be pressurised due to heat received from the environment. It also simplifies the piping arrangement and minimises piping and valves dimensions and system complexity. This again contributes to an increased safety.
The PNG carrier is based on known technology elements arranged differently. The vessel is a combination of an ordinary crude oil tanker and a container vessel while the containment system is based on ordinary pipeline fabrication principles. The cargo handling system is small in diameter with material and pressure rating that is well-known in the shipping and offshore industry.
COMPOSITE PRESSURE VESSELS / MODAL CONTAINERS
Trans Ocean Gas
Trans Ocean Gas is the only CNG proponent in the world that will use fibre reinforced plastic (FRP) pressure vessels to transport CNG by ship because, Trans Ocean Gas owns the patent rights to this method of CNG transportation.
FRP pressure vessels have been proven safe and reliable through critical applications in aerospace, in national defense, in the offshore oil and gas industry, and most importantly in public transit. The use of FRP pressure vessels overcomes all the deficiencies of proposed steel-based methods. The Trans Ocean Gas method using FRP pressure vessels is:
- Light weight (1/3 of steel);
- Corrosion resistant (thermoplastic liner);
- Safe from rupture (leak before burst)
- Highly reliable (probability of failure <10e-5);>
- Resistant to ultra-low temperatures (-80C); and
- Very cost effective
The cassette system also allows for 100 percent visual inspection while in service and the removal of condensed natural gas liquids at any point during a voyage. To ensure continuity of the corrosion resistant FRP bottles, the manifolds and piping network up to the first isolation valve are fabricated using duplex stainless steel.
Trans Ocean Gas intends to manufacture its FRP containment systems in Atlantic Canada. Trans Ocean Gas will license and lease its CNG systems to gas owners and entities that wish to transport bulk CNG. This will allow many countries and gas owners to economically transport their stranded natural gas reserves to new and existing locations for economic growth and development. Relatively little infrastructure will be required to gain access to this new source of energy through the Trans Ocean Gas CNG solution.
Since Trans Ocean Gas CNG is highly scalable, a wide range of gas production rates will prove viable. New or existing ships may be used to transport CNG using the Trans Ocean Gas method. High-speed voluminous container ship hull forms will make the most efficient FRP CNG carriers. Existing ships converted into FRP CNG carriers will have good short-term economics (e.g., for projects with a 10 year lifecycle). However, for CNG projects with longer lease terms, new ships may prove to be more cost effective. Trans Ocean Gas is also developing a barge-oriented solution for the Gulf of Mexico and other areas of the world that have relatively benign marine environments.
Floating Pipeline Company
The Floating Pipeline Company Incorporated too is building light-weight composite reinforced pressure vessels, known by the trade name of Gas Transport Modules (GTMs) [fact sheet, *.pdf], under license from TransCanada PipeLines Limited.
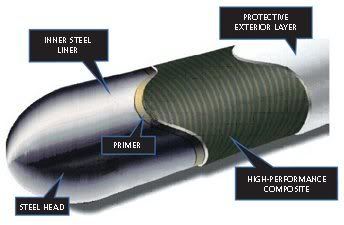
A manufacturing facility has been set up in a 120,000 sq ft building in the Port of Saint John, New Brunswick, Canada for the purpose of manufacturing of the GTMs and outfitting of ships, barges, rail cars and road trailers.
The GTM technology consists of wrapping a steel 'liner' with glass fiber, reducing the weight of a conventional all steel pressure vessel by up to 40% and implying that weight for weight, up to 40% more gas can be carried in the GTM. This offers significant transportation cost savings as well as benefits in rupture safety, strength, fatigue life and corrosion protection.
The use of GTMs in ships has received "Approval in Principal" from Lloyd's register and full approval of ship design will occur when each project is identified.
In the GTM system, a number ships shuttle back and forth between loading and unloading areas. The CNG is supplied by a compressor to the ship through high pressure loading connections and the process will be similar to the filling of a CNG tank in a vehicle, though on a much larger scale. In practice, at all times there will be a ship docked at the loading site and one at the unloading site.
At the loading site as one ship is nearing its maximum fill pressure of approximately 3000 psig, a second ship will be berthed and connected so that when the first ship is full, a seamless switchover is made to the second ship so the essentially continuous flow is maintained. The first ship then steams to the unloading site. At the unloading site, a ship is already connected to a pressure letdown station and potentially a compressor station and gas will be either flowing or compressed at a constant rate into the delivery system. When the second ship arrives, it berths and it is connected to the delivery system so that when the ship that is presently there reaches its minimum heel pressure of approximately 150 psig, a seamless switchover can be made to the full ship and constant flow is maintained. The empty ship is then disconnected and steams to the loading area for filling.
STEEL PIPE SEGMENTS
EnerSea Transport
Finally, EnerSea Transport has developed its socalled 'VOTRANS' cargo containment system, comprised of many CNG bottles made from large-diameter steel pipe segments. CNG tank modules are formed by manifolding groups of these CNG bottles together. This arrangement is inherently scalable and provides segregated gas storage.
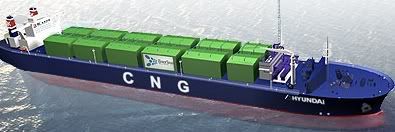
VOTRANS optimizes pressure and temperature to achieve improved storage efficiencies that are 60% to 100% greater than other CNG concepts. Lower operating pressure enables EnerSea to reduce wall thickness thereby increasing the volume of gas stored per ton of steel while simultaneously reducing total ship weight. The lower pressure also greatly reduces the compression and related fuel gas requirements for CNG vessel loading.
Gas is transferred into and out of these pipes using EnerSeaís proprietary gas displacement process, which is essentially an isothermal and isobaric operation. Other advantages of this process are:
- Increased utilization of the natural gas cargo due to a greater evacuation efficiency of the containment system which results in lower residual gas volumes (1% or less) for the return voyage compared to about 10% with high pressure blowdown systems.
- Accommodates a wide range of gas composition, including rich and associated gas
- Advanced instrumentation and controls provide highly reliable and redundant monitoring and management capabilities
The heart of EnerSea's ship-based marine gas transport service is its VOTRANS gas carrier . The V800 class vessel illustrates the VOTRANS base case design specifications (specifications, click to enlarge).
EnerSea has developed a range of vessel size classes, including the V600 and V1000 for smaller and larger transport needs, respectively, to provide clients with an optimum gas delivery solution. These vessels may be further tailored to confidently meet a project's unique and demanding field requirements, such as specific capacity, gas composition, sea state, and loading and offloading rates.
The vessel lightship draft was designed to ensure that the vessel could be constructed and the cargo containment system could be installed entirely in dry dock. This also allows the vessel to be dry docked in numerous ports worldwide for servicing and maintenance.
The vessel has been designed to ABS Class Rules for the ship's structure and marine systems while the cargo containment system has been designed using API, ABS, and IGC codes where applicable. The cargo loading and offloading systems have been designed to comply with IMO, API and ABS guidelines and rules as applicable.
EnerSea worked closely with its partners "K" Line, HHI, Paragon Engineering, and Alan C. McClure Associates to develop the vessel design and ship specification.
Biopact Team, 2007, CC.
References:
Market Wire News – Marine CNG Poised for Commercialization as Numerous Projects Reach Funding Stage, Conference to Examine Ramifications [*.pdf] – April 27, 2007.
International Marine CNG Standards Forum [*.pdf] - August 19, 2005.
Knutsen OAS Shipping: Pressurised Natural Gas A New Alternative for Natural Gas Transport [*.pdf], The Oil & Gas Review - 2004.
EnerSea Transport: Prototype Testing Validates EnerSea’s CNG Transport System [*.pdf] - November 15, 2005.
Haszeldine, R.S. "Deep Geological Carbon Dioxide Storage: Principles, and Prospecting for Bio-Energy Disposal Sites" [*.pdf], Special Issue of Mitigation and Adaptation Strategies for Global Change, Addressing the Policy Implications of Potential Abrupt Climate Change: A Leading Role for Bio-Energy - July 15, 2005.
Biopact: Pre-combustion CO2 capture from biogas - the way forward? - March 31, 2007
0 Comments:
Post a Comment
Links to this post:
Create a Link
<< Home