German IT firm uses biogas fuel cell to power server farm


Specifications of the biogas powered Hot Module:
- System efficiency: 90%
- Electrical efficiency: 47%
- Thermal output: 180Kw
- Electrical output: 238Kw
- Coupled heat-power-cooling system
T-Systems has been enthusiastic because the extreme efficiency of the biogas powered fuel cell has allowed it to cut energy costs. The overall thermal and electrical efficiency of the system - combining heat, power and cooling - adds up to more than 90 per cent. Traditional utility power generation plants often have a capacity below 40 per cent.
Bernd Kraus, Business Process Outsourcing chief at T-Systems, says that the company currently spends 29 per cent on energy. Without the fuel cell system, these costs would increase to 38 per cent by 2010. The biogas fuel cell system allows T-Systems instead to push down costs to 20 per cent by 2010. Costs of the project are €2.5 million, partly covered by a €1 million research grant by the German Ministry of Technology and Economy.
Energy costs at the server park are high and have been increasing steeply over the past years due to rising grid electricity prices. The servers devour more energy than all of T-System's other operations. Fifty per cent goes to cooling. Moreover, as new servers keep getting stacked on racks in the same space, cooling needs per cubic meter become bigger and bigger:

The biomethane for the project is produced by Schmack GmbH, a global biogas leader. The biofuel is produced locally - in Pliening near München - from dedicated energy crops. The crop in question is starch rich maize, the whole crop of which is utilized to generate approximately 5000 cubic meters of methane per hectare. This is enough methane to yield an equivalent of 50 MWh per hectare per year.
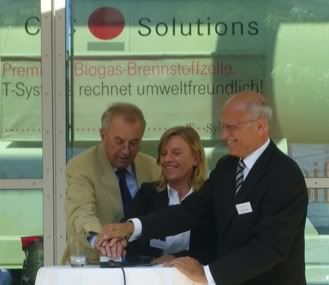
T-Systems-Manager Horstmann, Project coordinator Willi Hoffmann and State Secretary of Bayern Hans Spitzner push the button, activating the unique power system. Green and efficient computing power is now a reality.
To power T-Systems' entire data center in München with biogas, around 40 to 80 of the fuel cells would be required, says Manfred Teumer, T-Systems chief for Infrastructure & Architecture Services. One entire server farm requires around 1 square kilometer of biogas maize.
An advantage of the fuel cell system is that it yields a constant amount of energy, which is exactly what is needed for server farms that do not show sudden peaks in power consumption.
In case of power outages, T-Systems used to rely on its own diesel generators. But this is a thing from the past. By implementing a 'cross-cable' concept in the design of the fuel cell system, two fully independent power circuits are available all the time. In case the grid blacks out, the fuel cell takes over 100 per cent.
All images courtesy of Herman Gfaller, Silicon.de.
References:
Silicon.de: Bildergalerie: Brennstoffzelle im T-Systems-Rechenzentrum - August 30, 2007.
Silicon.de: Biogas fürs Rechenzentrum - T-Systems hat in seinem Rechenzentrum im Euro-Industriepark (EIP) München den Dauertest einer Brennstoffzelle gestartet - August 27, 2007.
Silicon.de: Geiz ist im Rechenzentrum geiler als Ökologie - August 17, 2007.
4 Comments:
Oh that's cute: the people running this site deleted my earlier comments because it disagreed with their agenda and, doubtless, source of profit.
In general, biofuels are bad because they take arable land away from being used for farming to being used to produce "biogas." I'm sorry, but I think feeding people is more important than generating electricity to run servers, as is the case in this article. Less than 10% of the farm on earth can be farmed, and using some of this land to make electricity is a disgusting waste.
As an ecologist, I can also tell you that your calling this server/corn cycle carbon neutral is a complete lie. The corn has to be fertilized every year and carbon emissions are made producing, shipping, and spreading this fertilizer. Carbon is also put out to pump water to the crops, presumably.
Biofuels are not environmentally friendly.
Robert, we deleted your earlier comment because it contained vulgar language.
You are welcome to discuss bioenergy here, but please keep things decent.
Kind regards,
Biopact team
What a wonderful idea! we burn the corn stovers ,we burn huge quantities of jute sticks,rice husks anyway as Agri waste-so there is no waste of cellulosic materials if we r able to use it to produce ELECTRICITY rather it is better usage of those Agri waste.In any case we have very limited source of inputs to generate Electricity in Bangladesh.
What a wonderful idea! we burn the corn stovers ,we burn huge quantities of jute sticks,rice husks anyway as Agri waste-so there is no waste of cellulosic materials if we r able to use it to produce ELECTRICITY rather it is better usage of those Agri waste.In any case we have very limited source of inputs to generate Electricity in [email protected]
Post a Comment
Links to this post:
Create a Link
<< Home