New biogas reactor for energy crops cuts energy costs, increases productivity

Farm-based biogas digesters of today are generally designed for the fermentation of liquid manure. Their use for energy crops is questionable, since these fibre-rich materials tend to build up a persistent float layer. In order to prevent flotation, agitation and stirring has to be intensified to a level where it demands up to 10% of the electric energy produced. Too intensive mixing can also affect the substrate decomposition process negatively. Moreover, when fermentation residues are discharged, the bacteria which stick to the biomass get lost as well, further reducing efficiency.
The new up-flow leach-bed process developed by the Leibniz agricultural engineers follows a completely different strategy by stimulating flotation in order to increase not only energy efficiency but biogas production rates as well.
The key component of this two stage process is a novel anaerobic leach-bed reactor (schematic, click to enlarge). Plant raw material is continuously fed to the reactor bottom and, after fermentation, removed from the top as solid residue. Gas bubbles generated by bacteria adhere to plant particles and thus, naturally induce floatation like in common digesters. Due to missing agitation inside the leach-bed reactor a liquid phase is formed and used as leachate. This leachate circulates upwards through the leach-bed reactor and downwards through a high rate anaerobic digester with immobilised bacteria. Volatile fatty acids are leached from the solids and efficiently converted to biogas in the high rate reactor. Excess bacteria are transferred to the leach-bed reactor enhancing solid degradation as well.
Experiments at laboratory scale (see below) reveal that compared with common farm-based digesters the reactor loading can be increased by at least factor two to three while yielding the same amount of gas. At significantly reduced energy demands the up-flow leach-bed process promises considerably increased productivity and stability as well as an uncomplicated and precise process control. The risk of overloading is practically eliminated:

As a next step testing of the patent pending system at pilot-scale (10 m³) is projected.
Background
Typical biogas digesters in use today can only deal with energy crops under certain conditions and often in an inefficient way. But precisely the use of dedicated energy crops such as specially designed maize or grass hybrids has become important for the production of renewable biomethane. When fermented in classic digesters, energy crops need continuous stirring, which takes up a considerable amount of energy. A 2005 study by the German Agency for Renewable Energy indicates that this may run up to as much as 10% of the energy produced by the plant.
Too intensive mixing can also affect the substrate decomposition process negatively. When fermentation residues are discharged, the bacteria which stick to the biomass get lost as well, further reducing the efficiency. As a consequence, a classic reactor digesting energy crops can only handle around 3 to 4 kilograms of organic dry matter per cubic meter of working volume and per day. Higher reactor loads lead to an inhibition of the decomposition process because of the build-up of volatile fatty acids.
The goal of the research at the Leibniz Institute for Agricultural Engineering therefor was to design a system that reduces the loss of bacterial biomass and increases the stabilty and efficiency of biogas production from dedicated energy crops. The researchers modified existing high-power fixed bed or mud bed reactors commonly used for the treatment of organically highly loaded industrial waste water.
In order to make such reactors suitable for the fermentation of renewable crops the organic materials must be liquefied first. Thus a two-stage and at the same time two-phase procedure was developed. An appropriate system, consisting of a fixed bed reactor in combination with 4 intermittently operating solid reactors was already developed and has found practical agricultural applications.
While such an intermittent fermentation process with a separate solid and liquid treatment phase is state of the art, the Leibniz Institute wanted to develop a continuous system for energy crops, which did not yet exist. The novel approach allows for a continuous mode of operation and offers substantial advantages. When the conditions inside the reactors are kept constant, a better adjustment of the micro-organisms becomes possible which results in an increased biological conversion efficiency by the bacteria. The new process also allows for much higher loading rates. Finally, a more balanced and continuous methanation simplifies the use of the biogas.
Laboratory tests
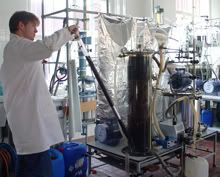

The process temperature was kept in the entire system to a thermophile 55°C. As substrates two different types of silage maize were used successively: Maize 1 ( dry matter = 33.1 %, organic dry matter = 96.7 % of DM) for 27 days, followed by Maize 2 (dry matter = 34.9 %, organic dry matter = 95.9 % of DM). In addition, to increase the fibrous nature of the substrate, barley straw was added (2 to 5 % of the total substrate mass).
On the basis of batch fermenting tests the methane-production potential of the organic matter of Maize 1 was put at 415 liter/kg-1, that for Maize 2 was 364 liter/kg-1 and that of the straw 334 liter/kg-1. During the tests the reactor load of the solids reactor was increased gradually, with the organic dry matter being increased from 6,3 to 16 gram/liter/day.
Besides other process variables, the most important parameter that was focused on was the generation of methane.
Results

After the addition of the substrate on day 60, a brisk decrease in methane production was observed. The allocation of the methane yield to the two reactors changed fundamentally when reactor loads were increased. The share of methane coming from the fixed bed reactor rose from an initial 10 % to 75 %. From this it is to be concluded that the solids reactor can handle a load factor of 6.3gram/liter/day organic dry matter without the need for a high-power reactor. For higher loads the use of a high-power reactor is essential.
On basis of these results, it is assumed that the high-power reactor can be reduced to a size 30 % smaller than that of the solids reactor. The fermentation speed of the solids with a hydrolysis constant of 0.14 day-1 was about 5 times higher than that observed during the fermentation of silage maize in traditional fully mixed, mesophilic plants.
The Leibniz Institute for Agricultural Engineering Potsdam-Bornim (ATB) is one of the leading European research institutes in the field of agricultural engineering. Production and use of biomass - not only for CO2-reduced energy production but also for material exploitation - including economic and ecologic assessment, are long term research issues at the ATB. Complete value creation chains are taken into consideration: from raw material to product i.e. from field to tank.
Graphs and schematics: translated and adapted by Biopact. Courtesy: Leibniz Institute for Agricultural Engineering Potsdam-Bornim.
References:
Leibniz Institute for Agricultural Engineering Potsdam-Bornim (ATB): Neues Hochleistungsverfahren zur Vergärung von Nachwachsenden Rohstoffen - Versuchsdurchführung, (text on the laboratory tests).
Leibniz Institute for Agricultural Engineering Potsdam-Bornim (ATB): Neues Hochleistungsverfahren zur Vergärung von Nachwachsenden Rohstoffen, (intro).
Leibniz Institute for Agricultural Engineering Potsdam-Bornim (ATB): Neues Hochleistungsverfahren zur Vergärung von Nachwachsenden Rohstoffen - Ausgangslage, (background).
Linke, B., M. Heiermann und J. Mumme (2005), "Ergebnisse aus den wissenschaftlichen Begleitungen der Pilotanlagen Pirow und Clausnitz." In: Trockenfermentation - Stand der Entwicklungen und weiterer F&E-Bedarf, Band 24, Hrsg. Fachagentur Nachwachsende Rohstoffe e.V. Gülzow, S. 95-102
Linke, B. und P. Mähnert (2005), "Biogasgewinnung aus Rindergülle und nachwachsenden Rohstoffen" [*.pdf],Agrartechnische Forschung 11 (5), S. 125-132
0 Comments:
Post a Comment
Links to this post:
Create a Link
<< Home