QuestAir to supply biogas purification systems to Swiss company

The green, climate-neutral gas can be made efficiently from the anaerobic fermentation of a wide variety of organic feedstocks, either derived from dedicated bioenergy crops (earlier post on biogas maize, grasses and grass hybrids)or from waste streams from agriculture, municipalities or industry.
An interesting development in the field of large-scale biogas production is that of feeding the gas into the natural gas grid. In Europe, several companies are already doing this (earlier post). In the same context, the concept of 'biogas corridors' is gaining attention (earlier post). It consists of the simple idea of establishing energy plantations and biogas plants close to existing natural gas pipelines, which can then be supplied with the green gas.
But for the idea to work, efficient biogas purification technologies must be developed. Depending on the biomass feedstock, raw biogas has methane concentrations of around 55 to 70%, with the remainder being carbon dioxide, water, hydrogen sulfide and particulates. For it to be fed into the natural gas grid, the biomethane must be scrubbed and reach methane concentrations of more than 96%. Once the purified green gas is mixed into the grid, end consumers of course do not note the difference, biogas can be used just like its fossil counterpart: in power plants, by households, in fuel cells or as a fuel for CNG-capable vehicles.
Several biogas purification technologies currently exist, with some interesting innovations being made. One of the innovators is Canadian company QuestAir Technologies Inc., which announced that it has received an order for its compact M-3200 'Pressure Swing Adsorption' system to recover pipeline grade methane from biogas generated by an anaerobic digester in Lavigny, Switzerland.
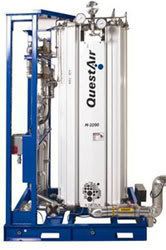
PSA is a commonly used technology for purifying gases. The technology was introduced commercially in the 1960's and today PSA is used extensively in the production and purification of oxygen, nitrogen and hydrogen for industrial uses. PSA is based on the capacity of certain materials, such as activated carbon and zeolites, to adsorb and desorb particular gases as the gas pressure is raised and lowered. PSA can be used to separate a single gas from a mixture of gases. A typical PSA system involves a cyclic process where a number of connected vessels containing adsorbent material undergo successive pressurization and depressurization steps in order to produce a continuous stream of purified product gas.
The operation of a simplified PSA process to separate methane from a feedstock gas containing impurities, such as carbon dioxide, carbon monoxide or water is illustrated in the diagram (see diagram, click to enlarge).
Conventional PSA systems used today in industry are made up of four to 16 large vessels, connected by a complex network of piping and valves to switch the gas flows between the vessels. Despite their widespread use in industry, QuestAir believes that large scale PSA systems suffer from a number of inherent disadvantages. These PSA systems typically operate at slow cycle speeds of 0.05-0.5 cycles/minute since faster cycle speeds would cause the adsorbent beads to float or "fluidize" in the vessel, causing the beads to wear and ultimately fail. To meet customer demands for capacity, conventional PSA systems must utilize large vessels to compensate for the slow cycle speeds, leading to higher costs and a large equipment footprint. The use of large vessels also means that these PSA systems are typically erected in the field, increasing installation costs. The network of piping and valves used in large scale PSA systems, with the associated instrumentation and process control equipment, also adds cost to the overall system. QuestAir's simplified PSA system is far more compact, modular and cost effective.
We focus on this technology, as it opens up very interesting opportunities for decentralised bioenergy production in the developing world, even though they are not to be realised in the immediate future:

Many countries in the tropics and the subtropics have a large potential both to recover biomethane from organic waste streams, especially in large cities, as for its productio based on energy crops and agro-forestry residues.
A compact biogas purification system like that of QuestAir, allows for a decentralised production scenario that results in high quality gas, capable of fuelling CNG-vehicles.
Compared to other 'first generation' liquid biofuels, biogas production is more energy efficient, it yields a greater amount of energy on a per hectare basis. With a modular, portable purification system now available, decentralised motor fuel production centres can be established in areas previously unreachable by ordinary fossil fuels (such as oil and natural gas).
Such a decentralised system would side-step the need to extend natural gas and oil pipeline grids, and instead could be established locally. CNG-capable fleets can be introduced in remote locations, and bought off the shelf without the need for modifications, as they would run on highly purified biogas.
Alternatively, a scenario of biogas exports is not unthinkable. Several liquefied natural gas (LNG) facilities are being build in the South (notably in Equatorial Guinea, Nigeria and Angola) wich, just like the existing ones (in Malaysia and Indonesia), could be supplied by purified biogas. This green gas would then be fed into the LNG plant and be shipped to world markets, where it would fetch premium prices because it is CO2 neutral and renewable.
Currently, the production costs implied under these scenarios are prohibitive, but the concept as such is feasible. With technological advances being made in the sector, which will result in steady decreases in production costs, these scenarios will become practicable. Not in the least given a future of 'peak oil and gas' and price-tags being put on carbon dioxide.
It will be interesting to follow up on the Swiss case first, and see how it develops. If successful, there is no reason for developing countries not to adopt similar technologies.
QuestAir's purification system has been purchased by Verdesis Suisse SA as part of a new plant that will recover methane from biogas generated by the anaerobic digestion of organic wastes at the Lavigny site. The methane recovery plant will be owned and operated Cosvegaz S.A., a Swiss gas utility, and product methane from the plant will be injected into the local natural gas distribution grid operated by Cosvegaz.
Jonathan Wilkinson, President and CEO of QuestAir said: “We are extremely pleased to secure our first sale into the European biogas market, which represents an exciting growth opportunity for QuestAir. We have seen growing interest across the EU in the use of renewable sources of methane to supplement or replace imported natural gas. In addition, government programs in several EU countries are promoting the use of biogas as a carbon neutral source of compressed natural gas (CNG) transportation fuel for busses and cars.”
“QuestAir’s methane recovery systems offer a compact solution for cost-effectively removing carbon dioxide and other impurities from biogas, recovering high purity methane for high value end-uses,” Wilkinson said.
Meanwhile, German scientists are developing bio-based biogas purification systems. They are looking into using micro-organisms and algae that feed on the CO2 contained in biomethane. Pilot trials show this concept to hold some promise (earlier post).
0 Comments:
Post a Comment
Links to this post:
Create a Link
<< Home