World premiere: biogas fuel cell powers and cools telecom server farm
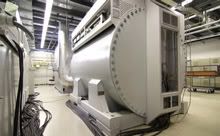
In a world premiere, a large server farm in Germany is overcoming the problem by using [*German, or here, *German] what is arguably the cleanest and most efficient energy system currently in existence: a fuel cell that delivers both electricity and cooling, powered by locally produced carbon-negative biogas.
Earlier we reported on the hyper-efficiency of biogas powered fuel cells, which are far more feasible than their hydrogen powered counter-parts because hydrogen production is either costly and energy intensive (if derived from renewables or nuclear) or dirty (when derived from fossil fuels) (earlier post). Biogas can be made locally from the anaerobic fermentation of (waste) biomass and used directly in the high-temperature molten carbonate fuel cell (MCFC). These innovatie systems normally function as highly efficient 'combined heat-and-power' (CHP) units. But using simple physics, heat can be transformed into cold.

The system consists of a 250kW fuel cell and a heat-absorber which regulates the entire power and temperature needs for the server suite. The power-heat-cold coupling forms a closed loop of interacting sub-systems resulting in an energy efficiency that is twice that of ordinarily powered cooling systems.
Whereas in large conventional utility power systems, some 60% of the primary energy is lost as heat, in the biogas-powered fuel cell the thermal energy is used for cooling the servers. The MCFC generates hot air, reaching temperatures of up to 400°C, which is transformed into cold air by the absorption chamber. This kind of synergy can not be achieved in classic (turbine) engine driven power systems.
Carbon-negative with biogas
Remarkably, this entire system is powered by biogas from energy crops. As such, the system is already highly energy efficient, but the use of locally produced biogas reduces its total primary energy inputs even further: no need to import fossil fuels. The city of München is investing in biogas production using locally grown biogas crops (in Europe, different high-yield and dedicated biogas energy crops are being developed, such as biogas 'super' maize, sudan grass and sorghum hybrids, or tropical grass species). Use of the biogas results in a carbon-neutral fuel cell system. When municipal waste is used the concept could even become carbon negative:

Power & Air solutions is buying the biomethane from Schmack Biogas AG, world leader in green gas production systems (earlier post). Schmack produces biogas in nearby Pliening, where it is purified (the CO2 removed) to a natural gas grade fuel. In Pliening, Schmack feeds the methane into the natural gas grid which brings it to München and to the server suite's fuel cell.
The fuel cell
The Hot Module is a so-called 'molten carbonate fuel cell' which in essence consists of a cylindrical steel vessel, a catalytic burner and a mixing chamber. As with all fuel cells, the electrochemical process is based on a reaction between hydrogen gas and oxygen, which delivers electricity and heat. In the Hot Module, biomethane and steam are introduced at the anode. A catalytic reaction transforms the mixture into hydrogen. During this process, electrons are released at the anode and flow towards the cathode. The electricity that is generated in the process is captured. At the cathode side, carbon dioxide and ambient oxygen react with the electrons to form carbon-ions. These carbon-ions then flow immediately through the electrolyte to the anode. This closes the electrochemical loop.
After RWE Fuel Cell acquired from MTU CFC Solutions, the company has become a fully owned subsidiary of Tognum GmbH. This firm develops stationary, biofuel capable fuel cells for the production of climate-neutral power and heat. Together with its American partner company Fuel Cell Energy, the firm has installed some 35 Hot Modules. The currently marketed high temperature fuel cells deliver a combined 245kW of electricity and 180kW of heat (in a combined heat-and-power configuration). The electrical efficiency amounts to around 50%, considerably above conventional power systems (the efficiency of which ranges between 25 and 35%). In the CHP configuration, overall systems efficiency increases to around 80%.
0 Comments:
Post a Comment
Links to this post:
Create a Link
<< Home