Large bio-oil experiment underway in China
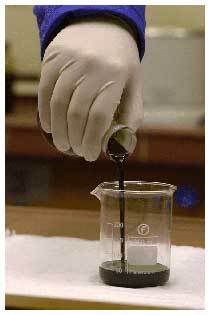
Professor Guo Qingxian of the Laboratory of Clean Biomass Energy at the UTSC, told Interfax that the experimental unit can produce 600 kilograms of oil per hour using straw as a feedstock, and the conversion rate of the unit stands at around 50 percent. Guo said that another critical experiment was needed to industrialize the project, which requires a minimal production capacity of 2 tons per hour.
Large number of applications
Bio-oil, or pyrolysis oil, is a renewable oil obtained when biomass is quickly heated in the absence of air (under a process called fast pyrolysis). It can be used as a substitute for fossil fuels to generate heat, power and chemicals. Short-term applications are boilers and furnaces (including power stations), whereas turbines and diesel engines may become available on the somewhat longer term. Upgrading of the bio-oil to a transportation fuel is technically feasible, but needs further development. Transportation fuels such as methanol and synthetic biofuels derived from Fischer-Tropsch gas synthesis can be obtained as well (the latter fall under the 'biomass-to-liquids' category of second generation biofuels). Furthermore, there is a wide range of chemicals that can be extracted or derived from the bio-oil:

Bio-oil is typically a liquid, almost black through dark red-brown, depending on its chemical composition and the presence of micro-carbon. The density of the liquid is about 1200 kg/m3, which is higher than of fuel oil, and significantly higher than of the original biomass. The viscosity of the oil varies from as low as 25 cP up to 1000 cP depending on the water content, the amount of light ends, and the extent to which the oil has aged. Due to large amounts of oxygenated components present, the oil has a polar nature and does not mix readily with hydrocarbons. It contains less nitrogen than petroleum products, and almost no metal and sulphur components.
Water is an integral part of the single-phase chemical solution. The (hydrophilic) bio-oils have water contents of typically 15 - 35 wt.%, which can not be removed by conventional methods like distillation. Phase separation may occur above certain water contents. It is reported that this phase separation does not occur until the moisture content increases above about 30 to 45 %.
Beneficial effects of the high water contents have also been reported, especially in the case of combustion. It causes a decrease in viscosity of the oil (facilitating transport, pumping and atomisation), it improves the stability, it lowers the combustion temperature and, as a consequence, it may cause a reduction of the NOx emission.
According to Gao, the heating value of the oil produced by the project reached around 40 percent of normal diesel, and the product could primarily be used to heat up boilers. Guo said that the Biomass Technology Group from the Netherlands now has a pilot bio-oil production project in Malaysia, with a production capacity of around 2 tons per hour. Guo said that little study had been made into the subject domestically and there was not a single industrialized project so far.
Applications of bio-oil
Many different applications have been developed or under developent for the use of bio-oil.
Heat Production
The heating value of bio-oil is lower than for fossil fuel, and a significant portion of the bio-oil consists of water. Nevertheless, flame combustion tests showed that fast pyrolysis oils can replace heavy and light fuel oils in industrial boiler applications. In its combustion characteristics, the oil is more similar to light fuel oil, although significant differences in ignition, viscosity, energy content, stability, pH and emission levels are observed. Problems identified in flame combustion of bio-oil are related to these deviating characteristics, but these can be overcome in practice. Bio-oil combustion in a boiler and / or furnace is shown to be the most straightforward approach for use of bio-oil. Meanwhile, bio-oil has been used commercially to co-fire a coal utility boiler for power generation.
Electricity production
Several hundreds of hours has been achieved in the last years on various diesel engines from laboratory test units to large size modified dual fuel engines. Test results mention positive results of engine performance in terms of smooth running. Nevertheless some problems still need to be resolved to use bio-oil to replace diesel, especially if the acidic nature of the oil (pH 3) and its tendency for soot formation and re-polymerisation is considered. The use of a bio-oil requires modification of various parts of the engine, amongst which the most important ones are the fuel pump, the linings and the injection system. Slight modifications of both the bio-oil and the diesel engine can render bio-oils a quite acceptable substitute for diesel fuel in stationary engines (CHP applications)
Experience with bio-oil combustion in gas turbines is limited. R&D projects known are those carried out by a Canadian company (Orenda), and Italian and German Research institutes. The potential is high, but there are technical limitations such as the fuel thermal stability, contaminants, and acidity. Non-conventional atomisers are required to account for the special properties of the oil. Ignition difficulties and significant carbonaceous deposits of unburned material inside the combustion chamber have been noticed. Nevertheless, commercially available gas turbines are said to be available within several years.
Synthesis gas
For the production of "green" hydrocarbons, only biomass can play a major role, because it is impossible to produce these from the other renewable sources. A comparison between the use of the solid biomass and the use of the liquid bio-oil as feedstock for synthesis gas production encourages considering gasification of bio-oil in large-scale syngas generation. In that case a conventional entrained flow gasifier can be used, which is proven technology. Apart from the scale-related considerations, another problem of solid biomass gasification is that the gasification conditions usually do not match properly with synthesis gas requirements:
* Direct biomass gasification is carried out at relatively low temperatures with air or with steam / oxygen mixtures, to avoid ash melting. The syngas produced therefore contains large amounts of nitrogen (when air is used), and high "tar" and methane concentrations. These "inert" compounds reduce the selectivity and reactivity of catalysts applied in further processing. Operation of a direct biomass gasification on pure oxygen requires steam to decrease the gasification temperature.
* Pressurization of biomass is expensive, and biomass gasifiers are yet developed for atmospheric conditions only. High-pressure syngas processing requires expensive syngas compression to 60 bar.
* The design of biomass gasifiers is different, due to the special requirements for the biomass-solids handling
Gasification of bio-oil with pure oxygen and further processing of the crude synthesis gas in Fischer-Tropsch processes may become technical and economic feasible. Experimental tests are carried out, gasifying bio-oil gasification with (enriched) air and pure oxygen.
Chemicals from bio-oil
Chemical components
More than 300 compounds have been identified as fragments of the basic compounds of biomass, viz. the lignin (amongst others phenols, eugenols and guaiacols), cellulose and hemi-cellulose derivatives (sugars, acetaldehyde and formic acids). Large fractions of acetic acid, acetol, and hydroxyacetaldehyde are reported in the analysis results. Until now, only 40 to 50 % of the oil identity (excluding the water) is revealed, but especially the large, less severely cracked molecules are not yet identified. All types of functional groups are present: acids, sugars, alcohols, ketones, aldehydes, phenols and their derivatives, furanes and other mixed oxygenates. Phenols are present in high concentrations (up to 50 wt.%).
Pre-treatment of wood can result in an increase of one particular component at the expense of the other. In wood-derived pyrolysis oil, specific oxygenated compounds are present in relatively large amounts. Basically, the recovery of pure compounds from the complex bio-oil is technically feasible but probably economically unattractive because of the high costs for the recovery of the chemical and its low concentration in the oil.
A large fraction of the oil is the phenolic fraction, consisting of relatively small amounts of phenol, eugenol, cresols, and xylenols, and much larger quantities of alkylated (poly-) phenols (the so-called water insoluble pyrolytic lignin). It showed good performance as adhesive for waterproof plywood.
Levoglucosan is a sugar derivative. Existing and potential applications and markets for biomass-derived LG are due to the possible self-polymerisation of LG, giving low molecular weight oligo- or poly-saccharides. Another anhydrosugar identified in the oil is the doubly dehydrated anhydrosugar Levoglucosenone.. Yields of LGS from cellulose can amount up to 24 wt.%. Another sugar derivate, hydroxy-acetaldehyde can be present in relatively large amounts in the bio-oil. It represents the smallest sugar, and can be used for the browning of foods.
Components that can also be derived from bio-oil are carboxylic acids. In the aqueous fraction of the bio-oil these acids are present in small amounts. Finally, furfural and furfurylalcohol are present in amounts up to 30 wt.% and 12 to 30 wt.%, respectively were produced.
Unfractionated bio-oil
The only commercial application of bio-oil is that of wood flavour or liquid smoke. A number of companies produce these liquids by adding water to the bio-oil. A red coloured product is then obtained that can be used as such to brown and flavour sausages, bacon, fish, etc.
The use of bio-oil or its water-soluble aldehyde fraction is investigated for the replacement of formaldehyde in urea-formaldehyde resins for particleboards. Due to the higher cross-linking of the lignin derived compounds in the bio-oil, a polymer with an improved strength can be obtained when mixed with conventional urea-formaldehyde resins.
Pure bio-oil can be mixed with lime to form BioLime . Injection of the mixture into flue-gas tunnels results in almost complete removal of sulphur oxides and a significant reduction of nitrogen oxides.
Reaction of bio-oil with ammonia, urea or other amino compounds produces stable amides, amines, etc. They are non-toxic to plants and can be used as slow release organic fertilisers.
Biomass logistics
Fast-pyrolysis offers the possibility of de-coupling (time, place and scale), easy handling of the liquids and a more consistent quality compared to any solid biomass. With fast pyrolysis a clean liquid is produced as an intermediate for a wide variety of applications.
As we reported earlier, several companies, amongst which a German consortium that impressed the Chinese government with its pyrolysis technology (earlier post), are attracting interest because of the modular pyrolysis plants they are developing. This kind of plants can be brought to the biomass source, instead of bringing the biomass to the plant (earlier post). This allows for a much smoother logistics: once the bulky solid biomass has been transformed into bio-oil with a higher energy density, it can be transported and distributed much easier.
Pyrolysis plants can utilize a wide range of biomass feedstocks, such as residues from forestry, agriculture or industry, as well as dedicated feedstocks. Recently, Thai experts have advocated the creation of vast eucalyptus plantations the wood of which would be used for the production of bio-oil (earlier post).
More information:
IEA Bioenergy Task 34 on pyrolysis.
Pyne: the Pyrolysis Network, a global network of research institutions devoted to the development of the technology.
The Dutch Biomass Technology Group.
The EU's ThermalNet, researching thermochemical biomass conversion processes such as gasification, direct combustion and pyrolysis.
0 Comments:
Post a Comment
Links to this post:
Create a Link
<< Home