From coal to biomass: Electrabel's world premiere
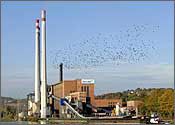
Currently some 13% of the world’s primary energy supply is covered by biomass. With environmental effects such as climate change coming to the forefront, people everywhere are rediscovering the advantages of biomass. Potential benefits include:
- Reducing fossil carbon emissions if managed (produced, transported, used) in a sustainable manner;
- Enhancing energy security by diversifying energy sources and utilizing local resources;
- Providing additional revenues for the agricultural and forestry sectors;
- Reducing waste (see the World Business Council for Sustainable Development. Biomass Issue Brief 2006)
Based in Belgium, Electrabel, 98.62% owned by French giant SUEZ, Electrabel had 15,794 employees and revenues of € 12.2 billion (US$ 15.5 billion) in 2005. All of Electrabel’s strategic decisions take full account of environmental protection and sustainable development. In converting the coal-fired plant in Les Awirs into one firing only biomass, Electrabel aims to:
- Manage its carbon dioxide emissions;
- Encourage the production of electricity from renewable energy sources;
- Obtain 300,000 green certificates that allow Electrabel to fulfill the obligation established by the Walloon Region and avoid paying penalties of some € 100 per lacking green MWh;
- Create the possibility of offering customers green electricity;
- Recycle the residual raw materials from forestry (the cultivation of forest trees for timber or other purposes);
- Diversify the fuels used to supply energy;
- Save fossil fuel reserves;
- Increase the share of green electricity from 15% to 18% within Electrabel Group.
In Les Awirs, near Liège in Belgium, Electrabel has retrofitted a pulverised coal power plant for using biomass as its sole fuel. This biomass is made up of pelletized wood dust that is again pulverised at the power plant. This method of producing electricity is a world premiere.
The production process comprises: production and supply of wood pellets, grinding these into wood dust on site and burning the wood dust using dedicated burners in the former pulverised coal boiler:

The biomass used is recycled forestry/wood conversion waste which otherwise would be lost and create useless greenhouse gas (GHG) emissions.
The biomass used in the plant comes from producers worldwide, but with a particular focus on local Belgian production in order to avoid transportation costs and environmental burden.
Results
The modification of this site has had a substantial impact on the surrounding communities and those involved in supplying the plant with wood pellets. It has:
-Created direct (local) employment on site for at least 10 years (duration for the grant of green certificates);
-Created indirect employment and economic development (forestry, wood pellets producer, shipping companies);
-Improved the quality of the local environment by reducing emissions in the air and road traffic required for waste product disposal;
-Recycled an industrial site, thereby maintaining local electricity production and creating the option to supply green electricity;
-Recycled the residual products from forestry, up to 350,000 metric tons per year;
-Avoided CO2 emissions of around 500,000 metric tons per year;
-Saved some 280,000 metric tons of coal annually;
-Added additional products to the company’s portfolio available to about 200,000 household customers (green electricity) while enhancing the company’s image (creating “goodwill”).
The plant has a net electric efficiency of 34% and is not a cogeneration plant that would have required getting access to a potential customer for the residual heat.
The market price of wood pellets today is about € 130/ton which makes it comparable to natural gas, but twice as expensive as coal.
0 Comments:
Post a Comment
Links to this post:
Create a Link
<< Home